Wire EDM
Wire EDM Cutting: Revolutionizing Manufacturing and Prototyping
Tailored Precision Machining Solutions for Every Industry Need
In the modern manufacturing landscape, precision, efficiency, and innovation are not just goals—they are imperatives. Amidst the myriad of technologies driving the industry forward, Wire Electrical Discharge Machining (Wire EDM) emerges as a cornerstone for those seeking to push the boundaries of what's possible in manufacturing and prototyping. This cutting-edge process, characterized by its ability to slice through hard materials with unparalleled accuracy, is transforming operations across sectors. From aerospace to medical devices, automotive to intricate tooling, Wire EDM is the key to unlocking new dimensions of precision and design complexity.
The Unmatched Precision
of Wire EDM
One of the standout features of Wire EDM is its extraordinary precision. It can achieve tolerances within a few micrometers, making it indispensable for industries where exacting standards are the norm. This level of accuracy ensures that components fit together flawlessly, perform as intended, and meet rigorous quality standards. Moreover, the ability to produce components with such precision reduces the need for subsequent finishing processes, saving both time and resources.
Complexity Made Simple
Wire EDM excels in manufacturing parts with complex shapes, intricate details, and sharp internal corners that would be challenging, if not impossible, to create with conventional machining. The process can effortlessly handle geometries that defy traditional cutting tools, opening up a realm of possibilities for designers and engineers. This capability not only enhances the aesthetic appeal of parts but also allows for the optimization of their functional aspects, leading to improved performance and innovation in product design.
Talk To An Expert
We can review your project needs and get an estimate to help you plan.
Quick
Turnaround Time
You get speed, flexibility and better control to produce special parts faster and with greater precision.
Machines Running 24/7
Our machines run around the clock to make sure we have every order on time and with the greatest accuracy.
Competitive Prices
With a large supply of metal always available, we are able to give competitive pricing to help lower costs.
High
Precision
Our precision EDM services are ideal for creating complex, high-accuracy components.
The Edge in
Prototyping
In the realm of prototyping, speed and accuracy are paramount. Wire EDM stands out by offering both, enabling rapid production of prototypes that precisely match the digital design. This speed-to-precision ratio accelerates the development cycle, allowing for faster iteration and optimization of designs. Consequently, businesses can shorten their time-to-market, staying ahead in competitive markets by rapidly evolving their product offerings.
Versatile Material Cutting With Advanced Wire EDM Services
Our Wire EDM services are not limited by material constraints. Whether you require intricate cutting on hard carbide or delicate shaping on lightweight aluminum, we have the technology and expertise to deliver with precision. Our commitment to versatility and quality makes us the ideal choice for projects across a myriad of industries.
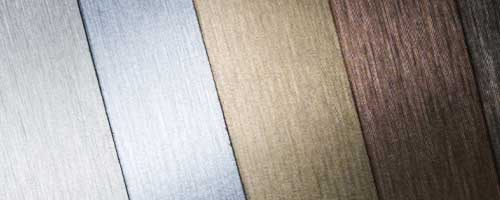
-
Carbide: The Powerhouse of Precision
Properties: Carbide is renowned for its extreme hardness and resistance to wear. It's often used in high-stress environments where durability is crucial.
Applications: Ideal for making precision molds, tools, and dies, especially in sectors like aerospace and automotive where robustness is key.
-
Aluminum: The Lightweight Champion
Properties: Aluminum stands out for its light weight, corrosion resistance, and excellent conductivity.
Applications: Widely used in aerospace for aircraft components, automotive parts, and electronic housings due to its lightweight nature.
-
Steel: The Backbone of Versatility
Properties: Known for its strength and malleability, steel is a go-to material for a wide range of industrial applications.
Applications: From automotive parts to construction tools, steel's versatility makes it a staple in various industries.
-
Alloy Steel: Enhanced Strength and Durability
Properties: Alloy steel, enhanced with elements like chromium, nickel, and molybdenum, offers improved strength and corrosion resistance.
Applications: Commonly used in automotive and aerospace components that require additional strength and endurance.
-
Heat Treated and Treated Steel: Peak Performance Under Pressure
Properties: Heat treating steel alters its physical properties, increasing its strength and making it more resistant to wear.
Applications: Ideal for parts that are subjected to high stress and temperatures, such as engine components and drilling equipment.
-
Titanium: The Strength of the Future
Properties: Titanium is lightweight yet strong, with high corrosion resistance and the ability to withstand extreme temperatures.
Applications: Extensively used in aerospace for aircraft and spacecraft parts, medical implants, and in high-performance automotive components.
-
Graphite: The Conductor of Precision
Properties: Graphite is unique for its high thermal and electrical conductivity, as well as its lubricating properties.
Applications: Used in the production of EDM electrodes, batteries, and as a lubricant in high-temperature environments.
-
Bronze: The Classic Alloy of Durability
Properties: Bronze, an alloy of copper and tin, is known for its toughness and resistance to corrosion and metal fatigue.
Applications: Commonly used in bearings, bushings, and gears, especially where resistance to wear and corrosion is required.
-
Brass: The Malleable Marvel
Properties: Brass, a copper-zinc alloy, is prized for its malleability, acoustic properties, and corrosion resistance.
Applications: Often found in electrical components, musical instruments, and decorative items.