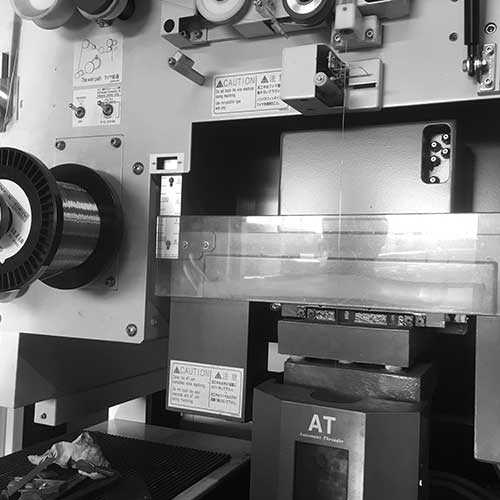
7 Essential Things to Know Before Integrating Wire EDM into Your Production
Integrating Wire Electrical Discharge Machining (Wire EDM) into your production can mark a significant leap in your manufacturing capabilities. Known for its precision and versatility, Wire EDM is a technology that can transform the way you approach complex manufacturing challenges. However, to fully harness the benefits of this innovative process, it's important to understand its intricacies and implications. Here are seven essential things to know before integrating Wire EDM into your production, offering a comprehensive guide to navigate this technological transition successfully.
- Understanding the EDM Process: Wire EDM is a method where a thin wire is used as an electrode to cut conductive materials with a series of rapid electrical discharges. This process allows for high precision cuts and is ideal for intricate or complex shapes that conventional machining can't handle.
- Material Considerations: The versatility of Wire EDM is one of its greatest strengths. It is particularly effective with conductive materials, including hard metals such as tool steel and exotic alloys. Understanding the range of materials compatible with Wire EDM will help you make the most of this technology.
- Design Requirements: Leveraging the full potential of Wire EDM requires thoughtful design planning. It is essential to understand that the process is especially suited for producing parts with tight tolerances and intricate details. Collaborating with a skilled EDM operator can help optimize your designs for the EDM process.
- Cost Implications: Integrating Wire EDM can be a cost-effective choice, particularly for specific applications such as low-volume production and complex prototypes.
- Surface Finish and Tolerances: One of the key benefits of Wire EDM is its ability to achieve superior surface finishes and extremely tight tolerances. This precision is particularly beneficial in industries where the quality of the surface finish and adherence to strict dimensional tolerances are critical.
- Choosing the Right Provider: Not all Wire EDM service providers are equal. Selecting the right provider is crucial for achieving the desired outcomes. Look for a provider with extensive experience, a solid track record, and the capability to handle the specific requirements of your industry.
- Long-term Benefits and ROI: While the initial investment in Wire EDM technology can be significant, it's important to consider the long-term benefits and return on investment. These include increased efficiency and the ability to produce more complex parts.
Conclusion:
Integrating Wire EDM into your production is a decision that can lead to substantial improvements in your manufacturing process. By understanding these seven key aspects, you will be well-prepared to make an informed decision and effectively utilize this technology. Whether you're looking to enhance precision, tackle complex designs, or improve efficiency, Wire EDM offers a path to achieving these goals. Embracing this advanced technology can position your business at the forefront of manufacturing innovation, ready to meet the challenges of today and tomorrow.