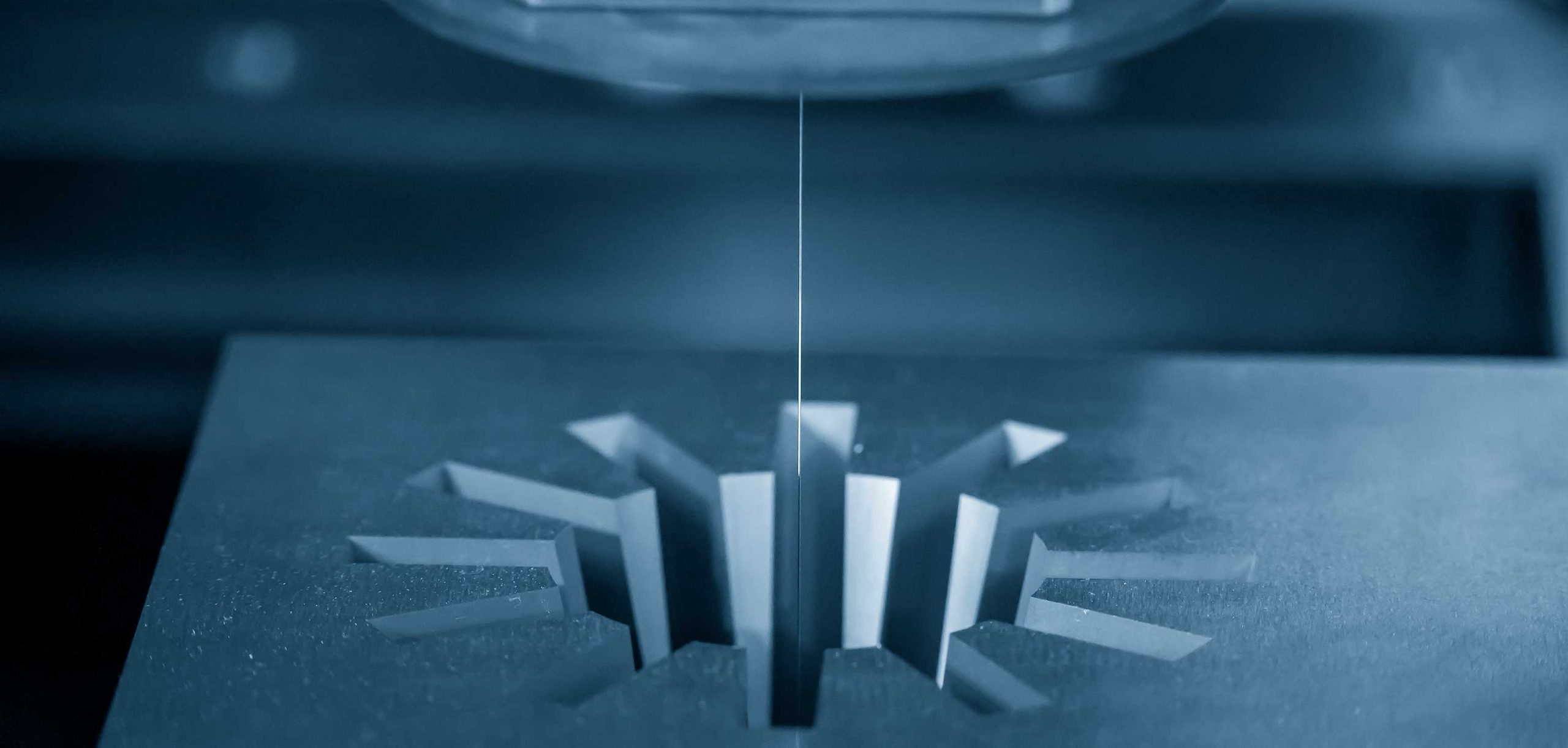
Wire EDM (Electrical Discharge Machining) is a specialized machining process known for its precision and adaptability across a wide range of materials. Unlike traditional machining methods that rely on direct contact between the cutting tool and the workpiece and create some wasted material in the cutting process, Wire EDM uses a thin, electrically charged wire to create intricate cuts. This non-contact approach allows for remarkably accurate and repeatable results, especially in high-precision industries.
Wire EDM cutting can be used on a wide variety of materials allowing designers to take advantage of the superior tolerance capabilities it offers compared to conventional machining methods.
Materials We Handle with Wire EDM
One of the primary advantages of Wire EDM is its ability to cut materials that are challenging or impossible to machine through traditional methods. Since the wire does not make direct contact with the workpiece, materials with high hardness or brittleness can be processed with ease. Here’s a look at some of the key materials we specialize in:
– Hardened Steels: Tool steels, stainless steels, and high-speed steels are commonly used in tooling, automotive, and aerospace industries due to their strength and wear resistance. Traditional machining can cause surface stress or thermal damage, but Wire EDM minimizes these effects, delivering smooth, precise cuts even in hardened materials.
– Tungsten Carbide: Known for its extreme hardness, tungsten carbide is commonly used in cutting tools and dies. Wire EDM provides a unique solution for working with this material, achieving accurate cuts and intricate geometries without risking fractures or imperfections caused by mechanical stress.
– Titanium: A favorite in aerospace and medical applications, titanium is strong, lightweight, and highly resistant to corrosion. Wire EDM allows us to machine titanium with minimal distortion and exceptional precision, critical for components where reliability and safety are paramount.
– Superalloys: These materials are highly heat-resistant and commonly used in turbines, jet engines, and other high-stress applications. Wire EDM’s ability to cut without generating high temperatures prevents heat-affected zones, preserving the integrity of the material.
– Exotic Metals and Alloys: Materials like molybdenum, copper, and brass are also suitable for Wire EDM. This versatility enables us to work with a broad range of industries, from electronics to medical devices, where different materials are required for specialized applications.
Holding Tighter Tolerances than Traditional Machining
Wire EDM is renowned for its ability to achieve extremely tight tolerances, often reaching accuracies as fine as ±0.0001 inches. Here’s why Wire EDM is superior for precision:
– Non-Contact Process: Since Wire EDM doesn’t physically touch the material, it avoids issues like tool deflection or material distortion caused by mechanical forces. This ensures that cuts remain consistent throughout the process.
– Thermal Stability: Traditional machining methods generate friction and heat, which can lead to expansion and dimensional changes in the workpiece. Wire EDM’s electrically charged wire eliminates significant heat buildup, maintaining thermal stability and enabling more accurate cuts.
– Complex Geometries with Precision: Wire EDM can produce complex contours and tight radii with exacting tolerances that would be impossible or cost-prohibitive with conventional methods. This precision is crucial for components with complex designs or critical fits, where even minor variances can affect performance. Next time you see Ideal Tool at a trade show, ask to see our beautiful metal jigsaw puzzles.
– Repeatability: For high-volume production, Wire EDM ensures each piece is identical, crucial for industries where consistency is vital, such as aerospace, medical, and electronics manufacturing.
At Ideal Tool, we pride ourselves on our ability to work with a diverse range of materials and to achieve tolerances that surpass what’s possible with traditional machining methods. Whether you need high-precision parts from hardened steel, titanium, or exotic alloys, Ideal Tool’s wire EDM capabilities provide a reliable, efficient solution for your most demanding projects. Reach out today to learn how we can bring precision and quality to your next project.