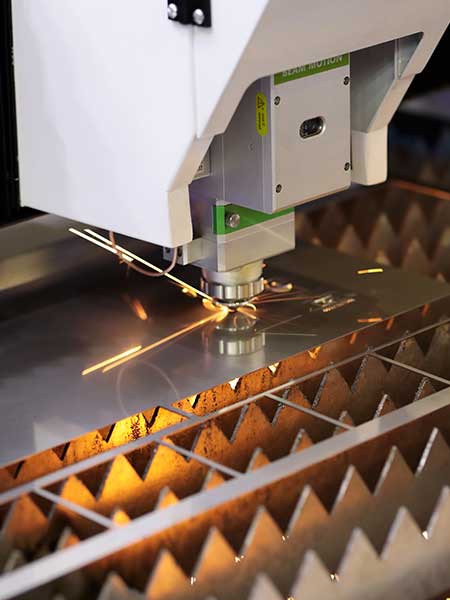
In the world of Wire EDM (Electrical Discharge Machining), each project is unique, and every component has its own specifications, tolerances, and requirements. At Ideal Tool, we specialize in tailoring our services to the specific needs of each client, whether they come from aerospace, automotive, medical device, or another high-precision industry. To achieve the quality and accuracy our customers expect, we need to start with a clear understanding of their requirements, which means reviewing their detailed part drawings and design ideas.
Each part design reflects the specific requirements of a project. These requirements can range from precise measurements and complex geometries to specific material properties and surface finishes. Some key aspects include:
– Dimensions and Tolerances: The dimensions of a component, down to fractions of a millimeter, are critical in Wire EDM. For some parts, especially in aerospace and medical industries, tolerances as tight as ±0.0001 inches may be required. When we receive a part drawing, we assess these tolerances to determine the level of precision needed and to confirm that Wire EDM is the ideal solution and that we are able to hold the needed tolerance.
– Material Specifications: Different materials respond differently in the Wire EDM process. For instance, working with titanium, tungsten carbide, or stainless steel require adjustments in power settings, feed rates, and cutting strategies. A part drawing, along with material details, helps us select the correct process settings to achieve optimal results.
– Geometrical Complexity: Many components require intricate cuts, tight radii, or non-standard shapes that are challenging for conventional machining. Part drawings allow us to analyze these geometries and determine the best way to achieve the desired shapes without compromising accuracy or causing unwanted stress on the material.
– Special Features: Some parts may include features like tapers, slots, or fine threads that are essential to the component’s functionality. When these details are specified in the drawing, we can use them to adjust our machine programming and make sure every unique element is precisely formed.
Without a detailed part drawing, it’s challenging for us to fully understand the scope and requirements of a project. Wire EDM is a versatile process, but knowing the exact specifications allows us to tailor our approach, ensure accuracy, and meet quality standards. By reviewing part drawings, the Ideal Tool team can quickly determine whether Wire EDM is suitable for the project. If certain features or tolerances are beyond the capabilities of Wire EDM, we can advise the customer on alternative methods or adjustments.
For customers, knowing the cost and timeline of a project is essential. Part of our quoting process involves reviewing the proposed part so that we can provide a precise quote based on the complexity, material, and tolerances. If certain design aspects can be optimized for Wire EDM, we can provide feedback and suggestions, often resulting in improved outcomes and potentially reduced costs.
When it comes to Wire EDM, every part is as unique as the drawing behind it. At Ideal Tool, we rely on these drawings to deliver custom solutions that meet the exact needs of each client. If you’re considering Wire EDM for your project, send us your part drawings and ideas—we’re here to help turn your specifications into precision-engineered reality. This approach ensures that we can provide the most accurate, efficient, and cost-effective service, tailored precisely to your design requirements.