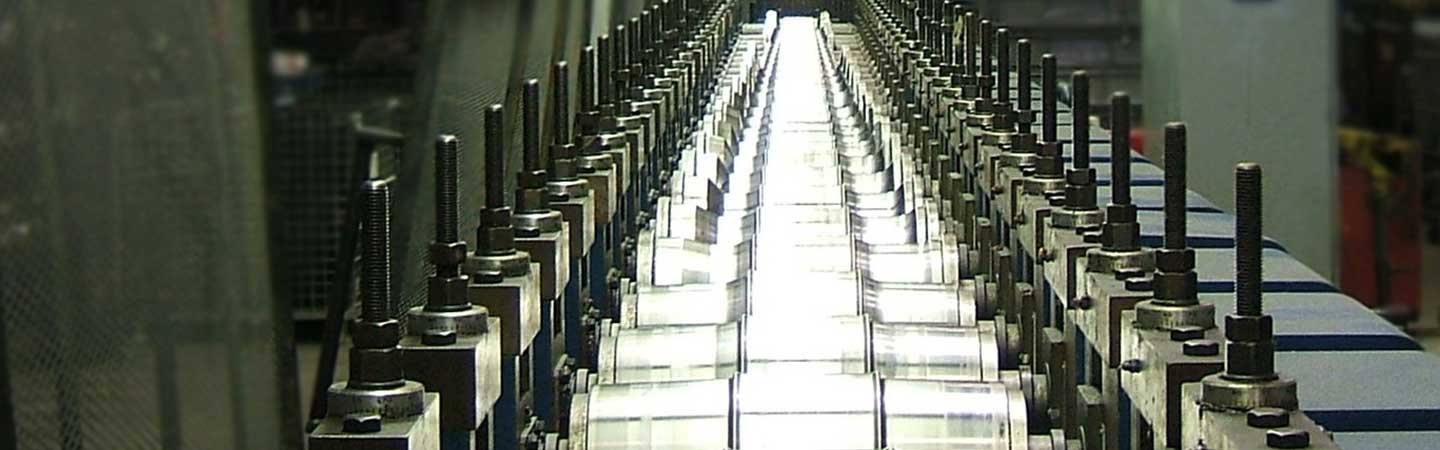
Wire EDM is a cornerstone technology for tool and die shops seeking to achieve unmatched precision and tackle complex designs. In a field where precision and durability are paramount, Wire EDM’s capabilities offer several distinct advantages for creating high-quality tools, dies, and molds.
1. Precision Cutting for Complex Die Shapes
Tool and die shops are often tasked with creating intricate shapes and contours that are difficult to achieve with traditional machining. Wire EDM excels at producing precise cuts with tolerances as tight as ±0.0001 inches, allowing for incredibly detailed and complex die shapes. For instance, progressive dies, compound dies, and transfer dies—used in high-volume stamping processes—require intricate geometries to produce precise parts repeatedly. Wire EDM makes it possible to achieve the detailed profiles and sharp corners that these complex dies require, ensuring that they operate accurately and consistently over long production runs.
2. Hard Material Processing for Durability
Durable tools and dies are typically made from tough materials like hardened steel, carbide, and titanium. These materials are chosen for their wear resistance and strength, essential qualities for components that withstand high-pressure stamping or injection molding. However, these same properties make them challenging to machine using conventional cutting methods. Wire EDM is particularly effective for hard material processing because it uses electrical discharges rather than mechanical force. This cutting process not only preserves the material’s hardness but also prevents tool wear and thermal damage that could compromise the die’s longevity and performance.
3. Producing Precision Punches and Dies
Wire EDM is ideal for producing high-precision punches and dies, which are essential components in stamping and forming operations. For example, when manufacturing automotive components, electronic connectors, or even household appliances, punches and dies must fit together with extreme accuracy to ensure the part is formed correctly without imperfections. Wire EDM allows tool and die shops to create punches and dies with precise dimensions, enabling them to achieve consistent, high-quality results in high-speed stamping applications. This precision also reduces the need for secondary finishing processes, saving time and costs.
For tool and die shops, Wire EDM offers the precision, flexibility, and efficiency needed to meet modern manufacturing demands. From creating complex die shapes to handling tough materials and supporting ongoing tool maintenance, Wire EDM enables shops to deliver high-quality tools and components that stand up to rigorous use. By incorporating Wire EDM into their operations, tool and die shops can produce the sophisticated tooling solutions that industries need to maintain accuracy, efficiency, and durability. For businesses looking to achieve cutting-edge results in their tooling projects, Wire EDM stands as a critical asset.